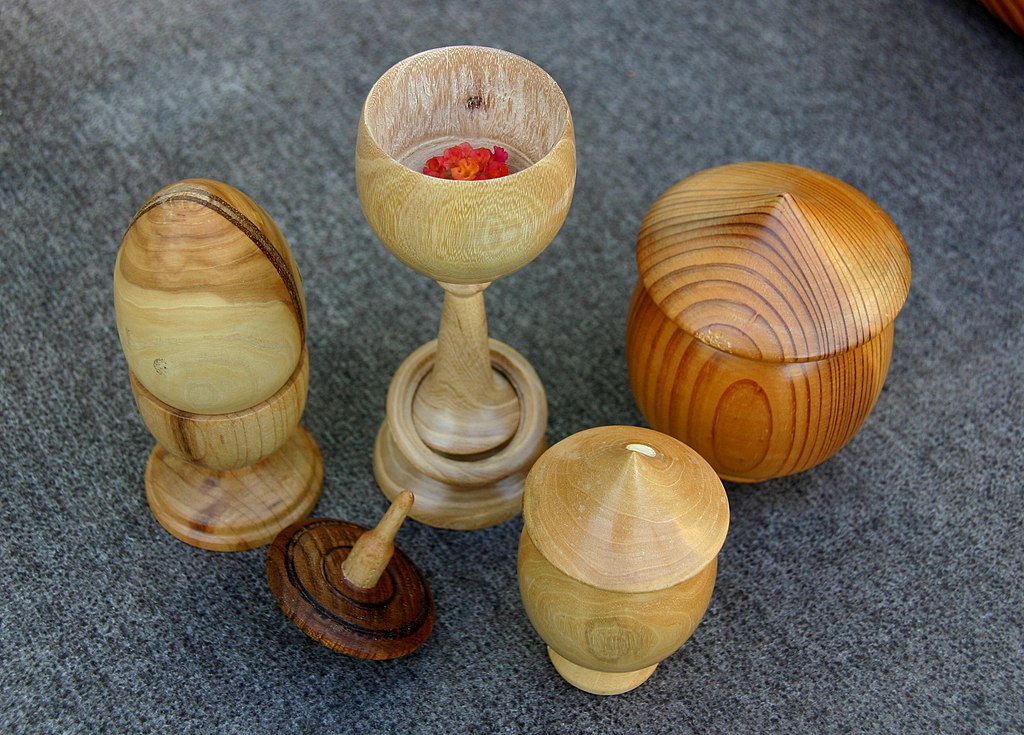
Philip Moulthrop first started turning wood in 1978, after his father Ed Moulthrop taught him the craft. He works with a lathe and a chain saw to remove the green leaves from trees that are sourced from the southeast. He then refines the bowl on the lathe, finishing it with several coats of finish. The entire process takes anywhere from four months to a year. Once they're done, you can either buy the bowls or give them as gifts.
Philip Moulthrop
Phillip Moulthrop Bowl is a beautiful red leopard maple vessel. For three generations, wood turning has been a family tradition. Philip Moulthrop’s bowls are not only their own creations but also part of several prominent museums' and private collections all over the globe. Below are some of the most well-known pieces. Continue reading to learn more about this talented artist.
In 1947, Philip Moulthrop, an American artist, was born. He started his education in general arts when he was just 20 years old and quickly developed a passion for woodworking. He purchased his first lathe when he was 16 years old and gradually increased his equipment. He created beautiful, turned vessels which attracted the attention and support of the arts community as well as the president of the United States. After his work had been recognized, he started selling his products at local craft shows and galleries. This earned him international recognition.
Matt Moulthrop
The Matt Moulthrop bowls are a wonderful example of Georgia's rich woodturning tradition. The artist was born and raised in Atlanta. He received his BA from Georgia Tech and MBA from Georgia Tech. While he did spend a few years in the 9-to-5 industry, he never lost passion for turning wood. He won national recognition for his bowls. His work is on display at ASU Art Museum, Carter Center, and Racine Art Museum.
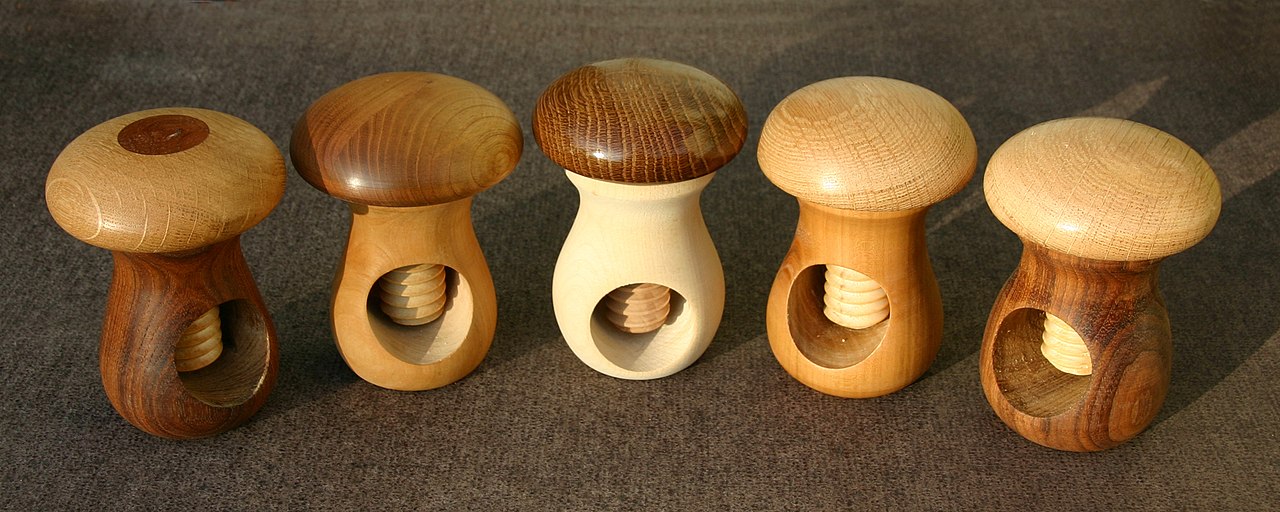
The Moulthrops are recognized for being world-class woodturners. They have works in many prominent collections in the United States as well as abroad. Moulthrop's own pieces are held in the Renwick Gallery of the National Museum of American Art. Collectors all over the world collect his bowls. During a recent Smithsonian photo shoot, he gave each photographer a signed copy of his family's book.
Ed Moulthrop
Moulthrop began turning bowls in the early 1970s and soon earned a scholarship to Princeton University to study architecture. Moulthrop spent a year in Vietnam and then resigned as an architect to pursue woodturning. His large-scale turn bowls, which were internationally recognized, are now held in prestigious museums such as The White House Collection of American Crafts and Museum of Arts and Design. These bowls are made of domestic woods and polished to a clear finish.
The Ed Moulthrop rare bowl measures nine by fourteen inches in size and is made from wild cherries. These wood bowls will be available for purchase at Gump's San Francisco. Ed Moulthrop's wooden pieces are also on display. Visiting the exhibition is the best way to discover the artisan's work. He also creates a gorgeous catalog of his work. Although you can purchase his bowls at museums, it's better to visit his studio to actually see them in person.
The Eagle & Phenix Dam Series
This limited edition moulthrop series features wood from Eagle & Phenix Dam. A series of dams that once stood near Columbus, Georgia. They are handmade by Philip Moulthrop, local artists. They can be viewed during regular museum hours. A portion of the bowls will also be available for bidding live.
The Moulthrop family is a key contributor to Georgia's wood-turned bowl industry. The Moulthrop family has been making bowls for over 50 years. Three generations have contributed to the creation of this museum. Many of these pieces are highly prized for their large size and smooth, polished surfaces. This exhibit features his mosaic bowl technique that involves glue and thin branches adhering to a turned dish.
Matt Moulthrop’s work
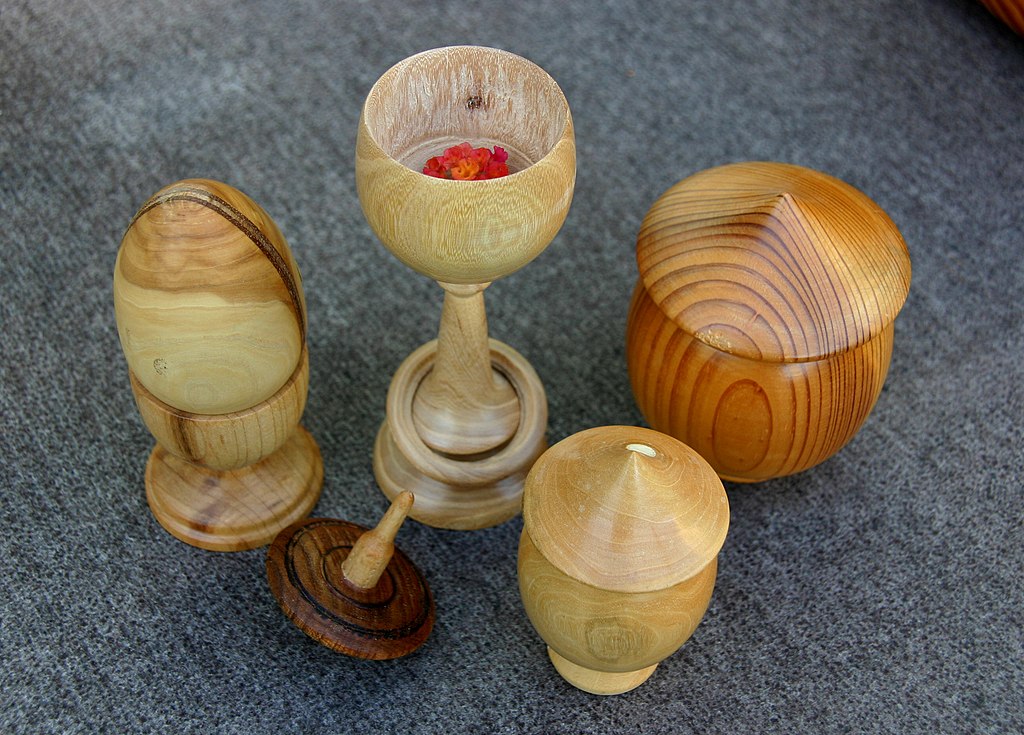
Matt Moulthrop was the son of Philip Moulthrop. His father taught him the art at a young age and the passion for woodworking grew from there. After completing his BA at the University of Georgia and his MBA at Georgia Tech, Matt turned wood as a career. He is now the third generation to make wooden vessels. His work is featured in many prominent art institutions including the ASU Art Museum and the Carter Center. He is currently in the process of creating commemorative pieces that will mark the 100th year anniversary of Georgia Tech Alumni Association.
The wood that he turns is not local to Georgia. To find unique wood, he travels all over the globe. He uses tools and a lathe hand-forged to turn trees from all over the globe. His pieces include wood that has been harvested from fallen trees in the Southeast, as well as exotic places like volcanoes and underwater forests. Check out his work if you enjoy it!
FAQ
How do I learn basic woodworking skills?
A great way to start learning how to build furniture is by building a simple bench for yourself. This project can easily be done using whatever wood you have at your house. If you're not sure which kind of wood to choose, you can purchase cheap pine boards at Lowes and Home Depot. After building your bench, sand off any rough edges and apply a stain or varnish.
How does a beginner woodworker earn money?
Many people are looking to create their own furniture and start an internet business. But if you're just getting started building furniture, there are other ways to earn money besides selling on Etsy. You could sell at craft fairs or local events. For those who want to build their own furniture, you might offer workshops. You might be able to offer services like remodeling homes or making custom pieces for clients if you are a skilled carpenter.
Where can I buy woodworking supplies?
You can find everything you need in many places. You could shop at your local hardware store or go online to Amazon.com.
You can also look for used furniture at flea markets or garage sales.
Statistics
- The U.S. Bureau of Labor Statistics (BLS) estimates that the number of jobs for woodworkers will decline by 4% between 2019 and 2029. (indeed.com)
- Most woodworkers agree that lumber moisture needs to be under 10% for building furniture. (woodandshop.com)
- Overall employment of woodworkers is projected to grow 8 percent from 2020 to 2030, about as fast as the average for all occupations. (bls.gov)
- In 2014, there were just over 237,000 jobs for all woodworkers, with other wood product manufacturing employing 23 percent; wood kitchen cabinets and countertop manufacturing employing 21 percent. (theartcareerproject.com)
External Links
How To
How to drive a nails in wood
To drive a nail into wood, the first step is to select the right size and type hammer. The most common types of hammers are claw hammers, sledgehammers, mallets, ball peen hammers, and hatchets. Each type of hammer has its pros and cons. A claw hammer works well when you're trying to hit nails with a heavy hammer. However it is difficult to precisely control where the blow hits. A sledgehammer allows you to hit large areas simultaneously, but it is too heavy and cumbersome to use for small tasks.
After choosing the right hammer, place your hand flat against the side of the head so that the handle rests comfortably in your palm. You can grip the handle with your fingers, but not so tight that it causes injury. Keep your wrist relaxed and the hammer straight up. Swing the hammer back towards the ground, with your aim at the middle of the nail. You should feel the impact of your hammer hitting the nail. Try practicing with a block to help you master the art of swinging a stick.
The hammer should be held close to your body when you are ready to begin driving the nail. Position the nail, so it's perpendicular to the surface of the wood. Keep your attention on the tip. Swing the hammer forward, and then move the hammerhead. Repeat this action several times, gradually increasing the speed of the swing. Once you've mastered the technique, try adding power to your swings. Then, raise the hammer from your shoulder to bring it down. You will be able to use more energy and put your best foot forward.
Once you've made the first nail hole, take out the hammer. Use a pry bar or screwdriver to pull out the rest of the nails. To avoid splitting the wood, make sure the nail heads are not touching the board's surface.